With the development of the world’s economic level, industrial product design requirements pay more and more attention to fashion, environmental protection, lightweight design, IMR process was born, and has been widely used in all walks of life, from the earliest consumer products such as laptop shells, cell phone lenses, home appliances, a variety of decorative panels, automotive dashboard, automotive interior parts, medical instrument panels, cosmetic boxes, children’s toys and so on.
What is IMR?
IMR (In-MouldDecoration by Roller): In-mold decoration technology is a technology that prints decorative and functional patterns on foil (film) through a high-precision printing machine, and then sends the foil through a high-precision foil feeding device into a special molding mold for precise positioning, and then transfers the patterns on the foil to the surface of the plastic product through the high temperature and pressure of the injection plastic material. The patterns on the foil are transferred to the surface of the plastic product.
IMR principle?
The pattern is printed on a layer of foil film, and the film is laminated to the plastic cavity for injection by feeding the film, and the ink layer with the pattern is separated from the foil film after injection, and the ink layer is left on the plastic part to get a decorative figure on the surface.
Production process of IMR process
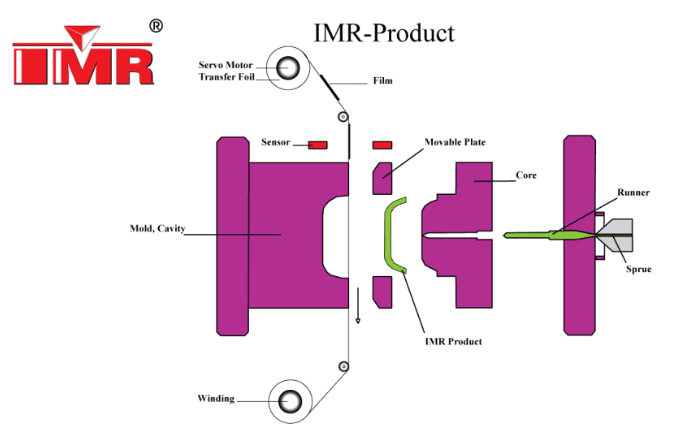
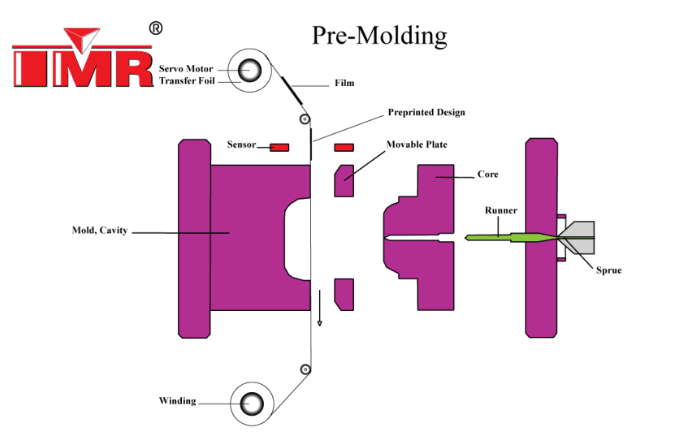
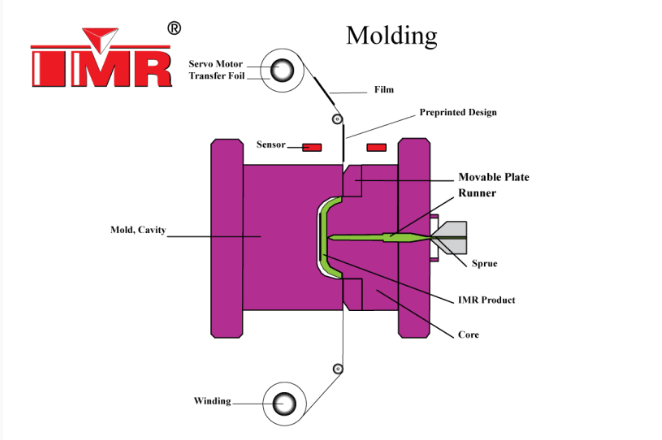
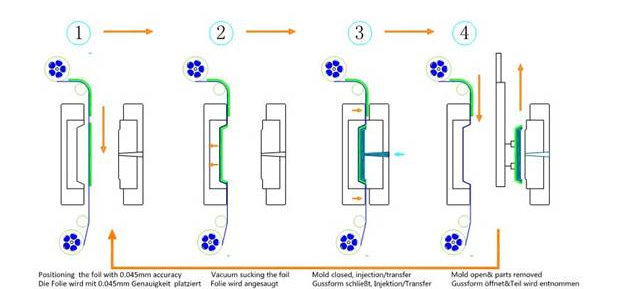
1. The press frame is open, and the transfer film is fed and positioned
2. Pressing the frame and sucking the vacuum to make the transfer foil fit into the cavity
3. Mould closing, injection moulding, thermal transfer and cooling and shaping at the same time
4. Open the mold, open the press frame, and remove the molded product while feeding the foil for the next round.
the advantages and disadvantages of the IMR process
1. Advantages of IMR process
1. One-piece molding, process simplification, reduce production/inventory costs and man-hours, shorten the product manufacturing cycle, and improve production efficiency;
2. The highest level of reliability testing in the industry, ensuring product stability and durability;
3. Highly automated production to ensure stable production with high yields;
4. Adopt automatic printing and environmental protection ink, in line with environmental protection requirements;
5. Multi-color printing, such as wood grain, carbon fiber, metallic color, etc. Product surface texture and pit pattern can be colored at the same time. For the transparent body parts, can make semi-transparent effect. With a three-dimensional texture;
6. Surface hardening (Hard Coat) treatment (up to 3H pencil hardness) has the characteristics of wear resistance and both beautiful.
IMR Product Features
IMR film has light weight, good light transmission, bright color and high brightness metallic texture. It can be widely used in high volume and high value-added products, such as cell phones, digital cameras, 3C peripheral products, MP3, mouse, DVD panels and cosmetic cases.
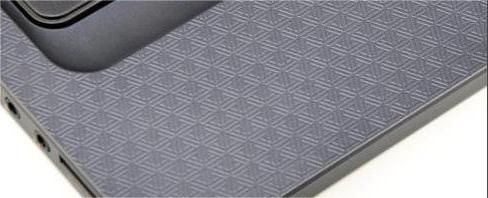
Cell phone manufacturers are particularly fond of IMR. Its products are practical, not only to meet the busy mobility needs of modern people, but also to increase the aesthetics of objects, in order to meet the changing social needs of the new era, and to enhance the use of various shades to meet the new sense of human vision. The IMR process meets the manufacturing needs of the 3C industry: fast production speed, stable yield, and low cost, which meets the needs of the 3C industry with high demand changes and short life cycle.


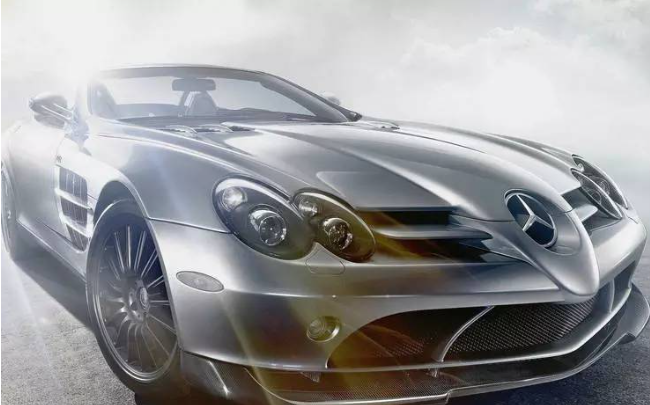
Development of new IMR technologies
1. New material development. Such as nylon material, etc.
2. Higher gloss; piano baking paint type high-gloss products.
3. Frosting effect (more than 20%).
4. Fingerprint resistance.
5. Different touch texture.
6. Semi-gloss and semi-mist combination products.
7. Part of the laser engraving type.
The future of IMR

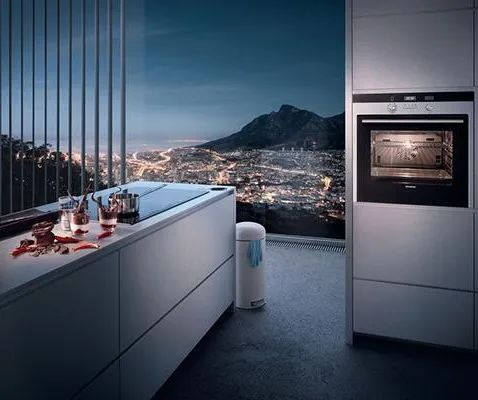
If, IMR technology can be applied up in more fields, then the shortcomings of traditional injection molding will be abandoned, integrated technology process, will greatly save time as well as process, at the same time the process is also the advocate of green environmental protection, to avoid the pollution brought by the traditional spray paint plating, but also can replace the traditional process 2-3 sets of mold products also come to the effect, so its cost is very competitive.